Liquid Penetrant Inspection (LPI)
OVERVIEW OF LPI:
Liquid Penetrant Inspection (LPI), also known as dye penetrant inspection, is a non-destructive testing method used to detect surface-breaking defects in non-porous materials. It is effective for detecting discontinuities such as cracks, porosity, seams, laps, and other surface-connected defects.
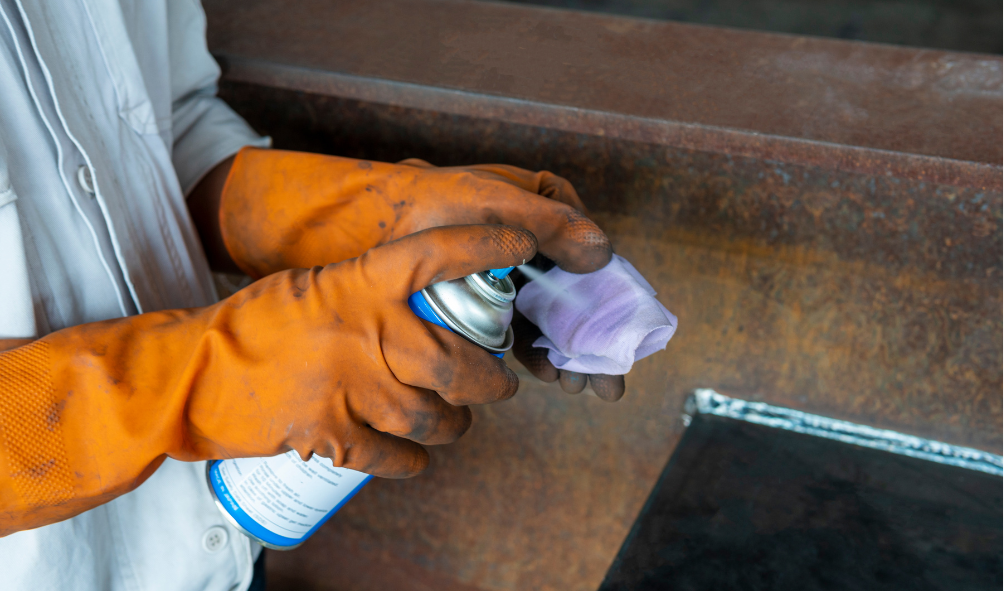
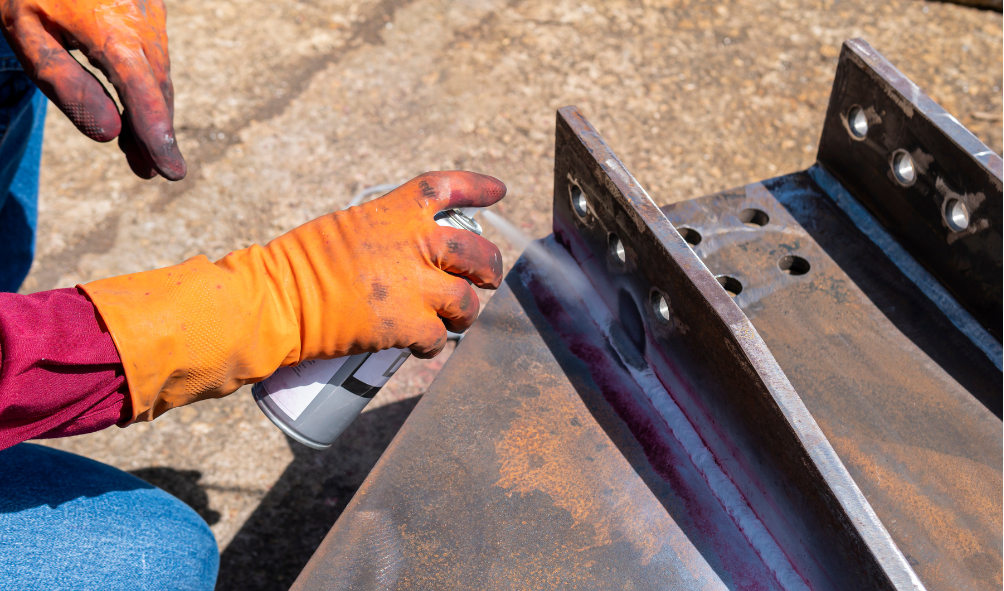
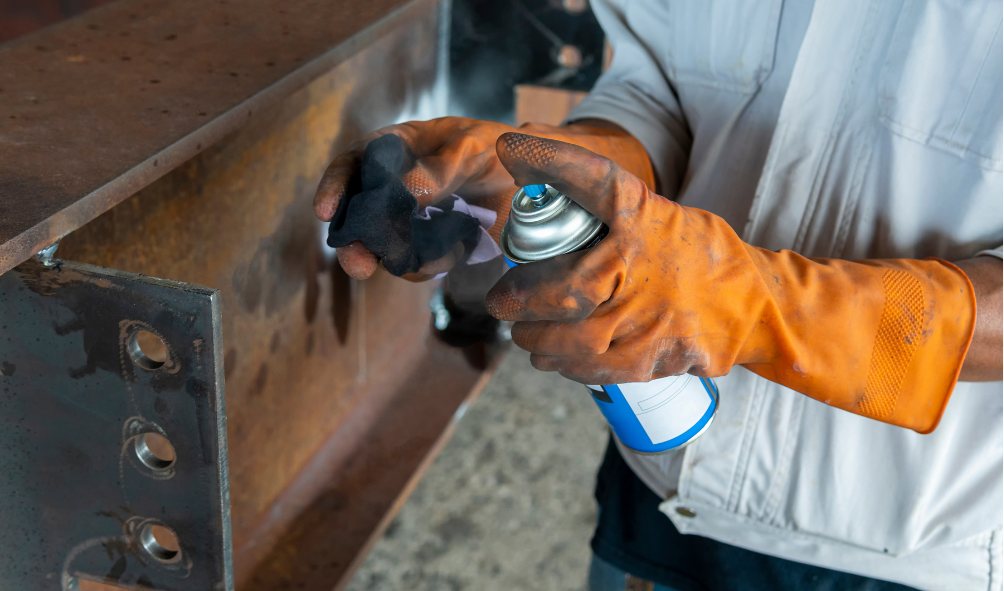
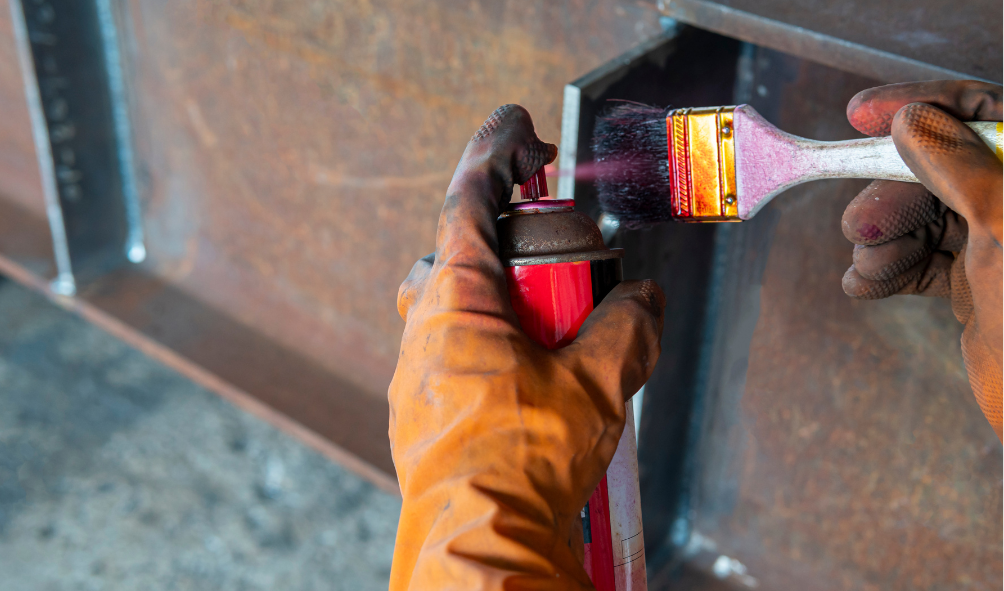
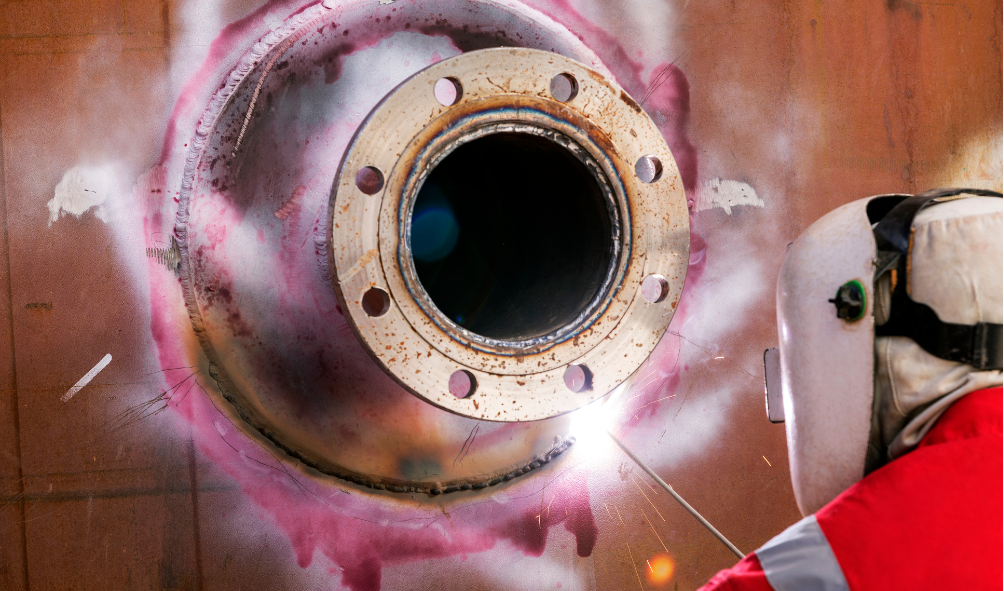
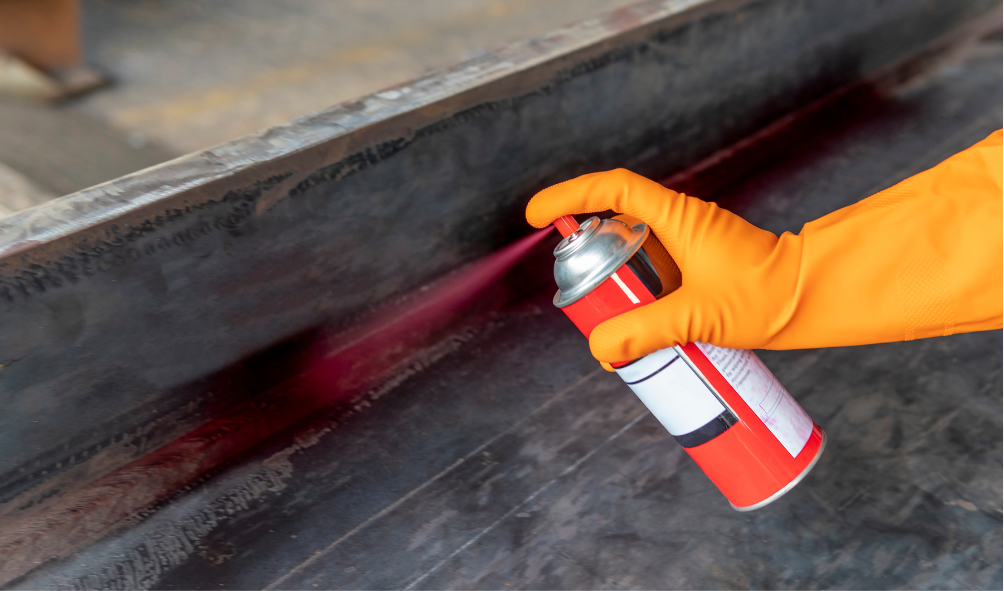
HOW DOES IT WORK?
The surface of the component must be thoroughly cleaned to remove any contaminants that might block the penetrant from entering defects.
A liquid penetrant is applied to the surface of the component. The penetrant is allowed to seep into any surface-breaking defects through capillary action.
After a suitable penetration time, the excess penetrant is removed from the surface.
A developer is then applied, which helps draw the penetrant out of the defects, creating a visible indication.
The component is visually inspected under appropriate lighting conditions (e.g., White light or UV light for fluorescent penetrants) to detect indications.
LPI is widely used in various industries, including aerospace, automotive, and manufacturing, to inspect components like castings, forgings, and welds.
- Highly sensitive for detecting surface-breaking defects.
- Applicable to a wide range of non-porous materials, including metals, plastics, and ceramics.
- Cost-effective and simple to implement with minimal equipment.
- Limited to surface-breaking defects; cannot detect subsurface flaws.
- Requires thorough cleaning of the component before and after the inspection.
- Not suitable for porous materials due to penetrant seepage.
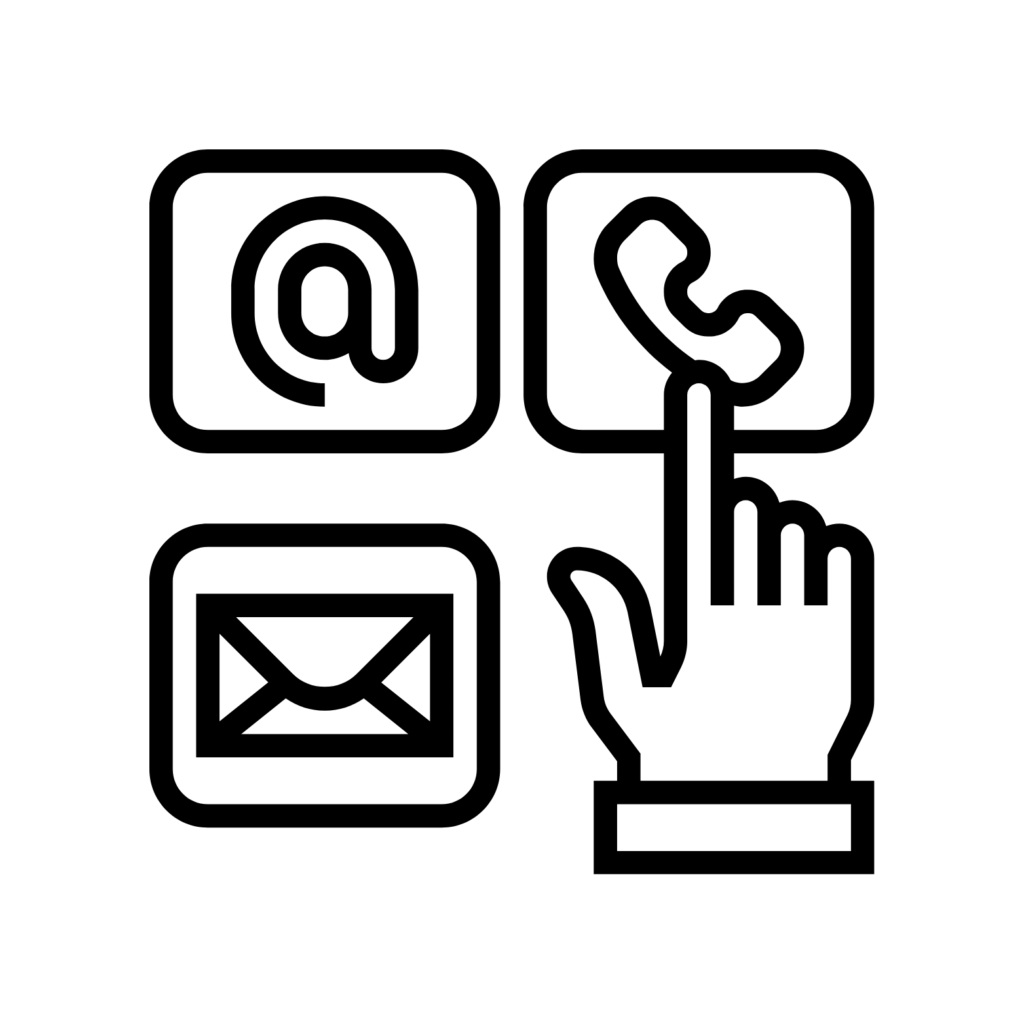
have any questions?
Send us an email at info@qindt.com.au or call us +61 468 937 996