Magnetic Particle Inspection (MPI)
OVERVIEW OF MPI:
Magnetic Particle Inspection (MPI) is a non-destructive testing technique used primarily for detecting surface and near-surface discontinuities in ferromagnetic materials like iron, nickel, cobalt, and some of their alloys. The method leverages the principle that magnetic fields can be distorted by discontinuities such as cracks, voids, or inclusions in the material.
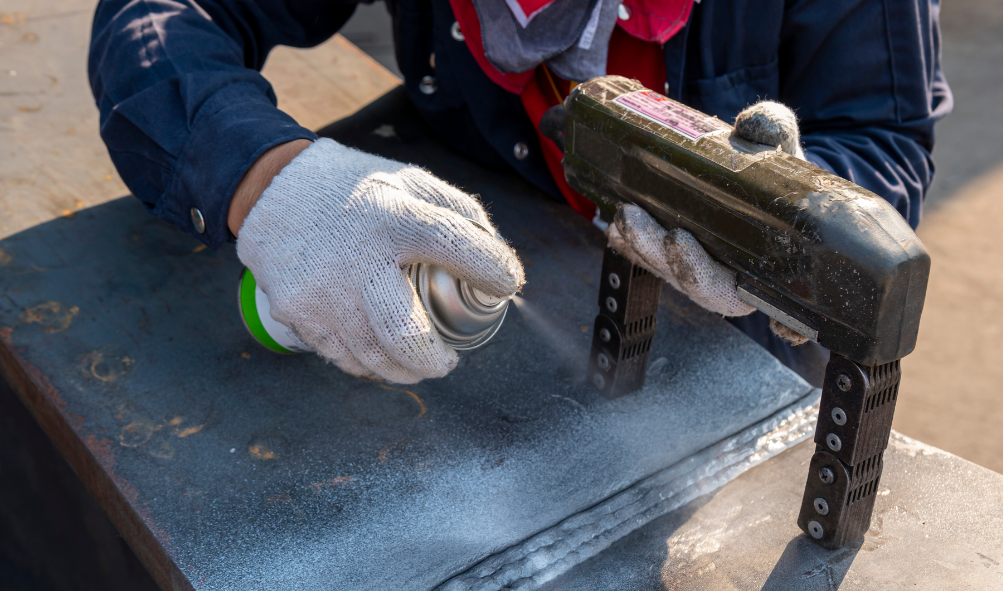
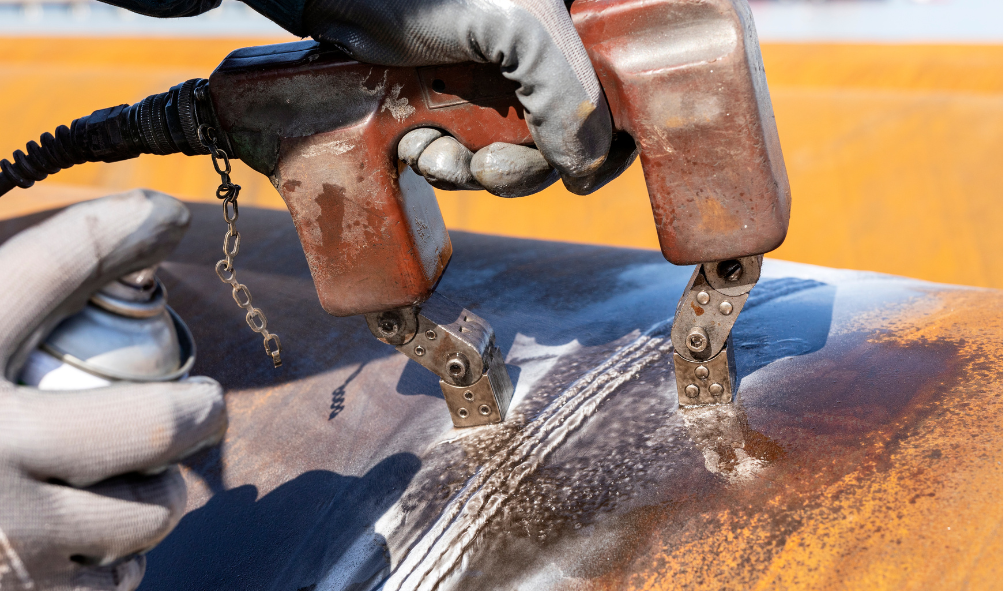
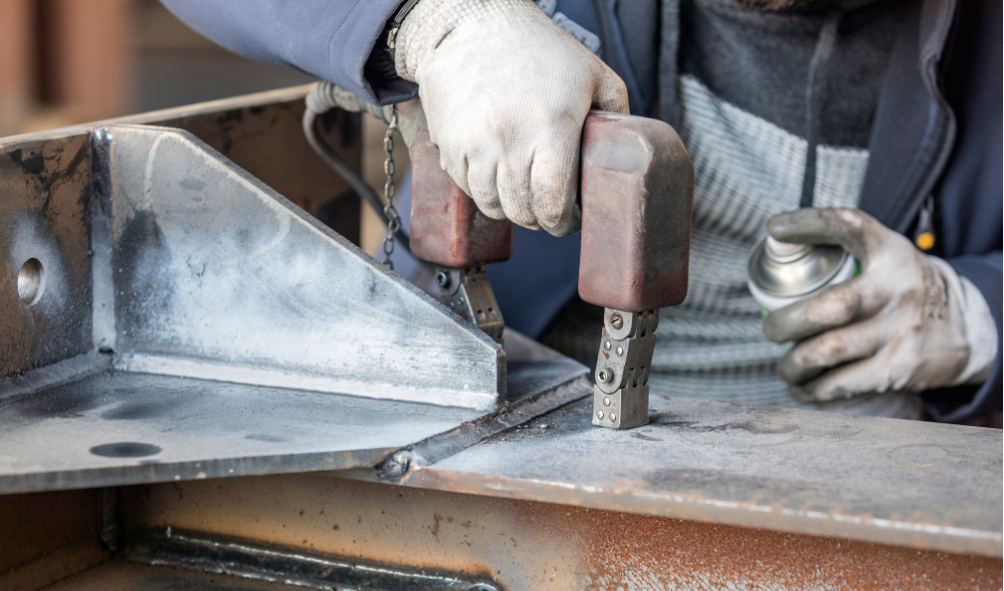
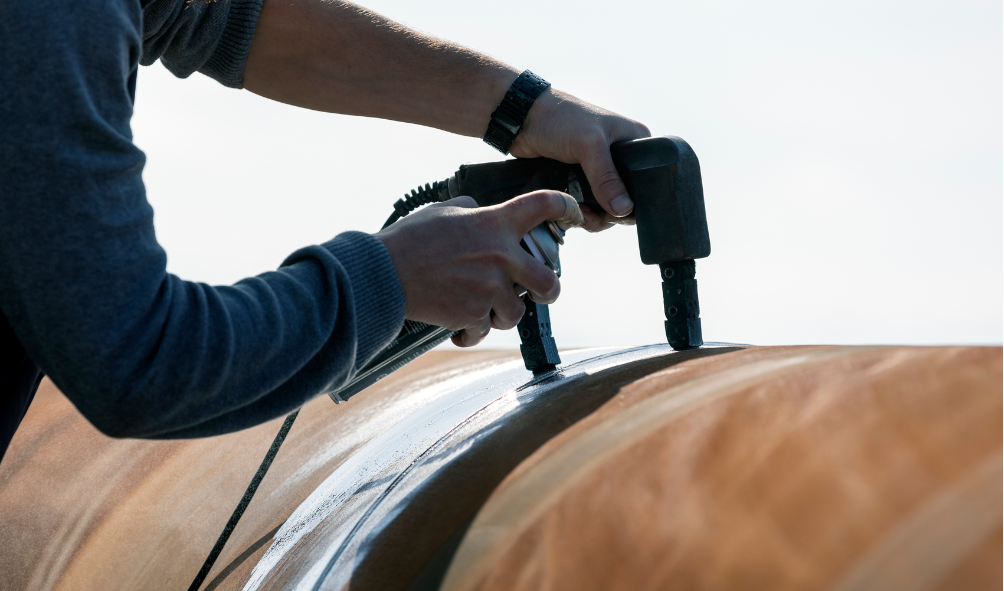
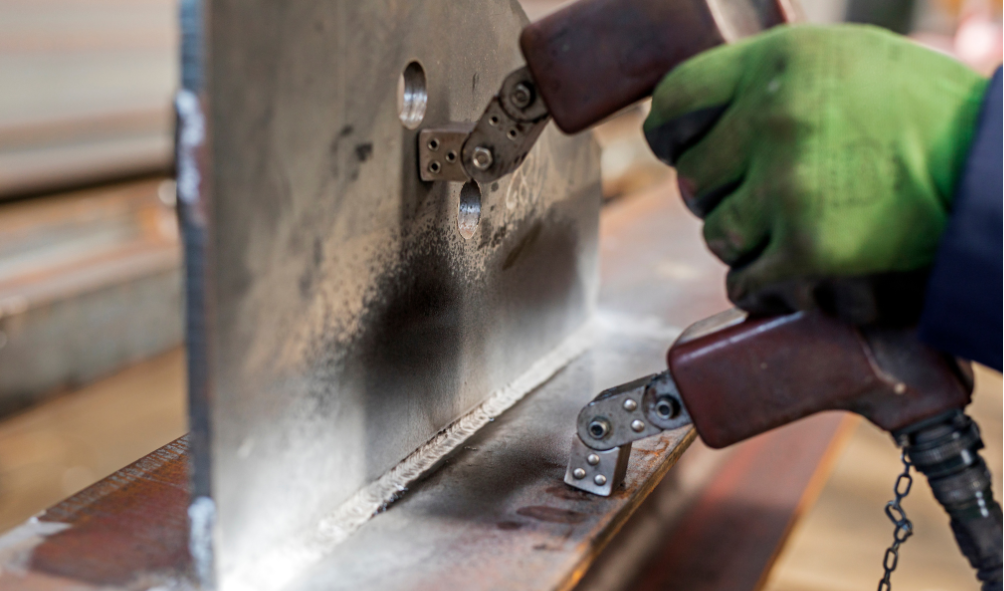
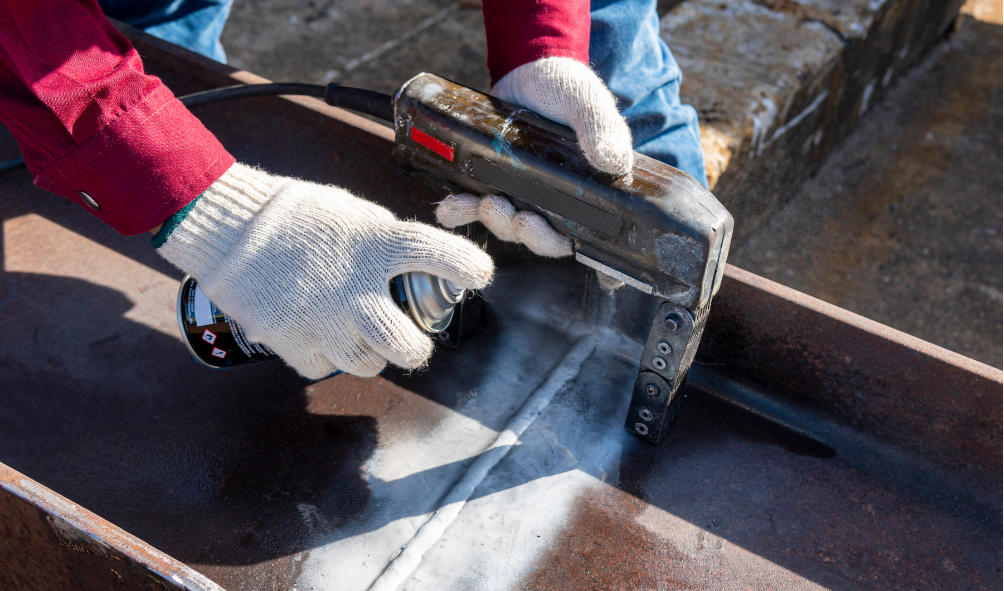
HOW DOES IT WORK?
The component to be tested is magnetized either by direct or indirect magnetization methods. Direct magnetization involves passing electric current directly through the component, whereas indirect magnetization involves placing the component in a magnetic field.
Finely milled magnetic particles, either in dry powder form or suspended in a liquid, are applied to the surface of the component.
If there are discontinuities in the material, the magnetic field will create leakage fields at these locations. The magnetic particles will accumulate at these leakage fields, forming visible indications that reveal the location, size, and shape of the discontinuity.
MPI is widely used in industries like automotive, aerospace, and power generation for inspecting critical components such as engine parts, pipelines, and structural welds.
- High sensitivity for detecting surface-breaking and near-surface defects.
- Can be used on large or complex-shaped objects.
- Relatively quick and cost-effective.
- Limited to ferromagnetic materials.
- Requires good surface preparation.
- Depth of detection is limited to near-surface flaws.
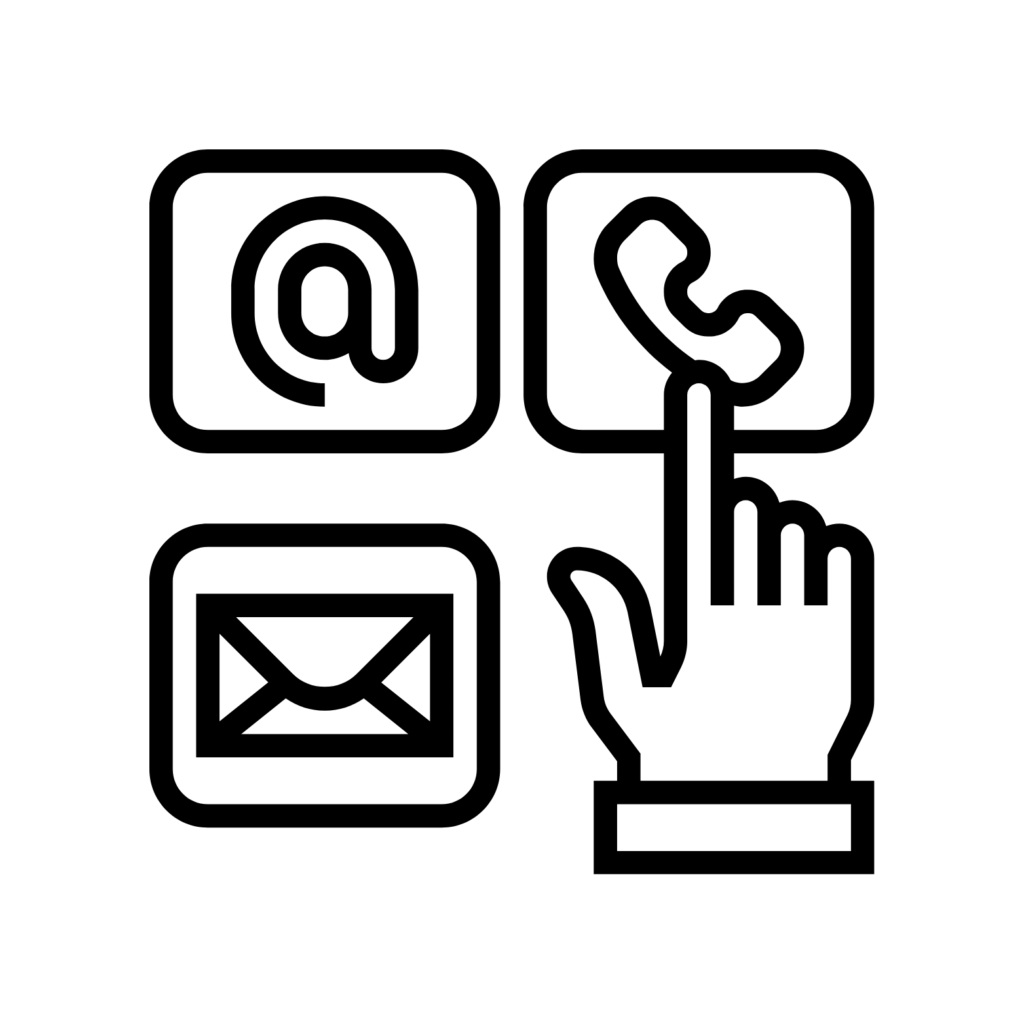
have any questions?
Send us an email at info@qindt.com.au or call us +61 468 937 996